Data management is the backbone of effective machine control. Having a consistent process in place for managing 2D and 3D files empowers machines to operate intelligently, efficiently, and reliably, while also supporting ongoing optimization and improvement efforts.
Here are seven best practices for machine control data management that can save you time, improve your workflows, and avoid costly delays.
1. Review the engineer’s CAD file
After you’re awarded a project, examine the engineer’s CAD file to determine if you’ll need to create a new model from the information provided. Whether the file is provided by the engineer, another 3rd party, or your firm, it’s your responsibility as the contractor to review the file and determine if it’s suitable for machine control. Be cautious, because if the file is not properly optimized for machine control, you may experience choppy blade control, a site that is not graded to plan or other issues.
2. Optimize data going out to the field
Initial CAD drawings from the engineer are typically provided as a single DWG file that contains multiple layers of information, such as the site layout, pipe diameters and cross-section views that aren’t scaled to real-world dimensions. Before sending files to the field, take a few moments to optimize them for your team.
Part of this process should involve removing data that means nothing to the machine operator or site layout team. This should reduce the file size and make uploading data faster and easier. Some 3D machine control systems make this process easy by allowing users to switch off layers and clip off parts of the project that aren’t relevant.
You might also need to update the linework colors. Keeping your linework colors consistent from project to project can help users more easily identify important information on the plan.
3. Keep your files organized and accessible
One often overlooked way to optimize project efficiency is making sure all files are well organized and accessible by key stakeholders. Cloud-based collaboration tools, such as Leica ConX, make this easy to achieve. In the ConX platform, you can manage all your connected construction projects and share job-related data with other team members or stakeholders.
One of the biggest advantages of a cloud-based platform is that files and subsequent updates to files can be sent directly to the machines over a secure connection, avoiding time spent driving to a jobsite and installing files from a USB drive. While USB drives can easily be lost, the files in ConX can be accessed from anywhere. ConX is also more secure than a USB drive since you don’t have to worry about exposure to multiple computers. In ConX, you can determine what level of access to provide individual users, further reducing risk.
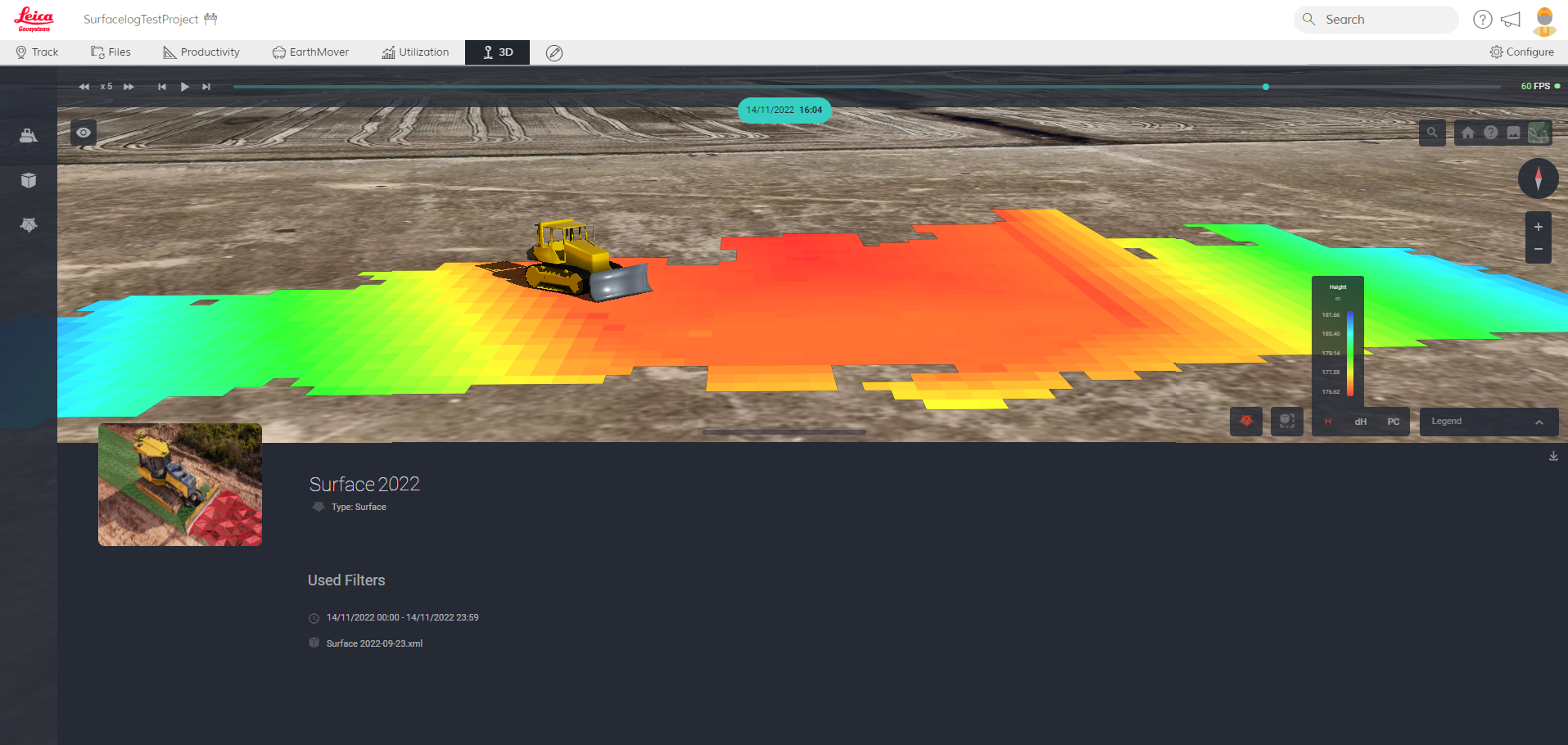
4. Create a localization file
A localization file allows users to work on a project with daily consistency by calibrating the digital plans to the location on the ground. It facilitates reporting local coordinates to grid coordinates and referencing different projects to a common coordinate system.
You can easily create a localization file using a service such as HxGN SmartNet. The service uses a mount point outside of your site’s control points so that even if your control point is lost, you can go back to ConX, boot up HxGN SmartNet, and continue to work.
5. Set up a geofence around your project
As new machines enter the project area, your operators need to know whether any files need to be updated. Setting up a geofence using a cloud-based collaboration tool such as ConX is an easy way to automate this flow of information.
6. Back up your files
Making backups of data files is critically important. If a file is inadvertently deleted, corrupted by a virus or inaccessible in the case of a power failure or natural disaster, having backup files will save time, money and a lot of headaches.
7. Send as-built data to the office
As-built data on a project is used to help determine production rates and billing for the volumes of earth moved. Using a consistent code for all as-built data will ensure clarity for both field and office personnel.
Your machine control system should have a way to easily capture as-built data and send progress reports back to the office on the work being done. If not, it might be time for an upgrade or a switch to a different technology manufacturer.
Keep It Easy
With the right technology, machine control data becomes infinitely easier to manage, back up, and control. Everyone from the field personnel to the office is on the same platform, yet you can manage the data so no one is overloaded with information they can’t use. Ease-of-use is what sets high-value machine control technology apart from other systems.
Need guidance on finding the right machine control technology for your needs? Contact us to talk to a knowledgeable subject matter expert.
Mike Rausch is a technical sales specialist for Leica Geosystems, part of Hexagon. He has been a specialist in construction positioning for the past 10 years.