A recognized BIM evangelist and early adopter of virtual design and construction, Raul Gomez understands the true value of building information modeling.
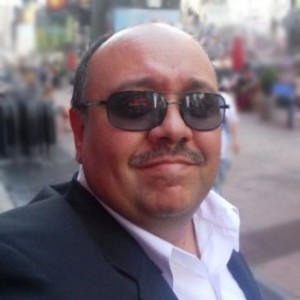
Gomez began his career in the late 1980s, when the industry was in the earliest stages of BIM (though it wasn’t called “BIM” then). Firms were just beginning to adopt intelligent modeling, moving from manual drawings to CAD.
When Autodesk Revit software entered the marketplace in 2000-2001, the design and construction process really began to improve with the introduction of tools that removed the “CAD minutia.” This allowed architects and engineers to think like architects and engineers, Gomez said.
“It became easier for designers to think like designers,” he said. “A 3D model was the core for design and the output became 3D drawings, sections, elevations and schedules. I was so passionate about this technology that I really wanted to spread the word.”
Gomez spent the next decade traveling the world as a consultant, “sharing the good news of BIM” and teaching designers and general contractors how to implement and execute Revit. In 2010, he joined Robins & Morton in Alabama, one of the top healthcare contractors, to help the firm integrate BIM and became one of the first in the industry to implement VDC processes as an organization.
“Today, we utilize the model not just for design, but also for model interrogation of the design, making sure the design is constructible in addition to reducing change orders and increased scope clarity,” said Gomez, who is now executive director of virtual design and construction (VDC) at Robins & Morton. “We also have our subcontractors involved to bring them into the fold and are using robotics to take intelligent, accurate information to the field.”
Robotic Total Stations Increase Efficiency
One of the biggest benefits of using tools like the Leica iCON robot 50 robotic total station, Gomez said, is the elimination of the manual key-in of coordinates and the linking of Autodesk Point Layout models directly to the robot, which enables everyone to operate more efficiently.
Information from design models can be utilized throughout the entire process for things like material cost trending. Rather than just looking at a printed set of windows on one floor of a hospital, designers can now model extract building components for all windows on all floors, allowing real-time design feedback.
“It allows us to be focused on design challenges, bringing a higher level of quality to owners and giving us the ability to think through what we are delivering,” Gomez said. “It really made us smarter as an industry.”
Another added benefit is the ability to streamline processes and design to be able to prefabricate offsite, Gomez said. Today, Robins & Morton prefabricates 40-50% of what it builds offsite and ships it to the field to install. This year, they should surpass operating in a complete BIM process and lifecycle 75% of the time and will reach 100% by 2017.
BIM and VDC Are Essential for Success
Robins & Morton began its formal BIM initiative in 2007. Adopting BIM and VDC has been essential to remain successful in the competitive healthcare industry.
“From a general contractor perspective, most firms started with BIM around the same time, so to we had to embrace the technology in order be competitive,” said Gomez. “It allows us to continuously improve.”
Today, Robins & Morton requires subcontractors to be BIM proficient and has spent the past several years educating subs to ensure they evolve with BIM. Robins & Morton has one of the largest training centers in Birmingham and invites subcontractors in-house to learn how to use BIM and VDC process in addition to Revit model training – all free of charge.
“Beginning in 2007, on every project, we worked with our architects, engineers and subs. They learned from us and now play a key role in our process of reviewing and coordinating models,” said Gomez.
Gomez added that though there was initial skepticism around BIM with some subcontractors, it has been short-lived.
“It always takes the first project for them to see the benefit, but once they’ve tasted BIM, they never go back,” he said. “If there was any pushback, it was when it was initially presented, but now everyone knows BIM is simply the price of doing business.”
At Robins & Morton, BIM is also part of the request for proposal (RFP) process.
“Part of our prequalifying of subcontractors is to review and analyze a firm’s abilities with BIM and they are scored on their capabilities,” Gomez said. “I am now beginning to see our subcontractors have the necessary skills and knowledge of BIM in-house.”
Robins & Morton uses Leica iCON robotic total stations for construction layout. A new internal training program has been established to teach additional teams how to use the software and equipment.
According to Gomez, BIM is quickly moving into an era where it will no longer be optional.
“There was a time we drew our construction documents by hand, when people said CAD would never catch on and they were either forced to use it – or had to use it – in order to remain competitive,” said Gomez. “The truth is that the significance of moving from manual drawings to CAD carries the same level of significance as moving from CAD to BIM and those companies that fail to adapt will become less and less competitive. I have two sons at Auburn University in Building Science, and BIM has become second nature to them. I believe the next generation of graduates who have been exposed to these programs from early on will be the nail that finalizes the adoption of the technology in our industry.”