Some commercial construction professionals still view laser scanning mostly as a clash detection or coordination tool. For VDC leader Joshua Marriott, those applications are just the start.
“I think it’s an industry-wide perception. When people hear BIM (building information modeling), VDC (virtual design and construction) or laser scanning, they immediately think 3D model or clash detection,” observes Marriott, who is the director of VDC and Field Solutions for The Weitz Company, #85 in the 2024 ENR Top 400 Contractors and the oldest general contractor west of the Mississippi River. “That insight is huge, of course, but point cloud data is so much more than that.”
Take bid pursuits, for example.
Winning Pursuits Through VDC
Weitz’s VDC team plays an increasingly prominent and early role in bid pursuits. There’s a growing recognition that the insight gleaned through early scanning helps make an even more powerful case to owners. It also gives the pre-construction team a running start on decisions surrounding budget, schedule and worker allocations. For example: Does the project fit our scope? Will we make money?
“My VDC team helped with over 120 pursuits this year (2024),” the 25-year industry veteran reports. “We have five people who are dedicated nearly full-time to pursuit support.”
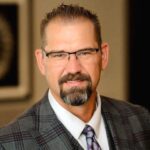
“By incorporating laser scan data into our presentations, we show clients we have thought about what is needed and we are willing to outwork our competitors.”
—Joshua Marriott, Director of VDC and Field Solutions, The Weitz Company
It usually starts as a brainstorming session. How can VDC add value to the pursuit? “We lean on our laser scanning expertise for projects involving existing structures, tie-ins, or expansions to gather precise data about the facilities,” Marriott says. “This information is important for creating accurate 4D visualizations demonstrating our project plans. By incorporating scan data into our presentations, we show clients we have thought about what is needed and we are willing to outwork our competitors. Our team carefully evaluates each project — whether it’s greenfield or brownfield — to suggest the best technology solution to the pursuit requirements.”
Once the project is in the win column, pre-construction commences with estimators. That means taking a deeper dive into project details, using point cloud data for as-built modeling, volume calculations, material quantification and any documentation that helps mitigate rework, change orders and margin erosion.
The technology proves valuable for complex projects where stakeholders are geographically dispersed across the country or globally. Point clouds and multidimensional data have become critical tools, enabling effective communication and collaboration between designers and trade partners while ensuring all team members clearly understand the project scope.
Rapid Technology Expansion Drives Innovation
“We fly our drones and do LIDAR scanning,” Marriott explains. “We use some of the newer take-off tools for quantification from the models. Our scans are extremely valuable to estimators as they communicate with subcontractors, equipment and material suppliers, and other vendors.”
Using scan data eliminates misunderstanding and creates more accurate measurements and quantifications. While traditional methods often rely on someone with a tape measure taking a few key measurements that could be off by inches, laser scanners capture billions of measurements with sub-centimeter level accuracy. This approach ensures everyone has access to precise, accurate information.
The imperative for laser scanning has evolved quickly at Weitz. Marriott started there five years ago. At that time, the company only had two VDC experts and zero scanners. Today, the group has nearly 20 technologists, and it is expected to possibly double in size in the coming years.
“It’s quickly become the way we build,” Marriott says. “That goes for many of our peers, too. My counterparts at other GCs have typically doubled or even tripled the size of their VDC departments over the last four or five years. We’re all leveraging scanned point cloud data and other VDC applications.”
Concurrent Coordination Accelerates Project Delivery
The VDC expert also sees growing technology sophistication from owners. To illustrate, Marriott cites a project at the University of Florida:
“The university is a savvy client. They know what to expect during a project and the value of scanning. For example, they asked for a high LOD (level of detail) model on a building — every pipe, nut and bolt modeled in a Revit file. That’s a major undertaking, with lots of time, people and expense. We showed them how scanning throughout the construction process would reveal even more detail with far less expense.”
“They were ecstatic,” he adds, “University officials wanted data before everything got covered up by ceiling tiles, concrete slabs and cladding.”
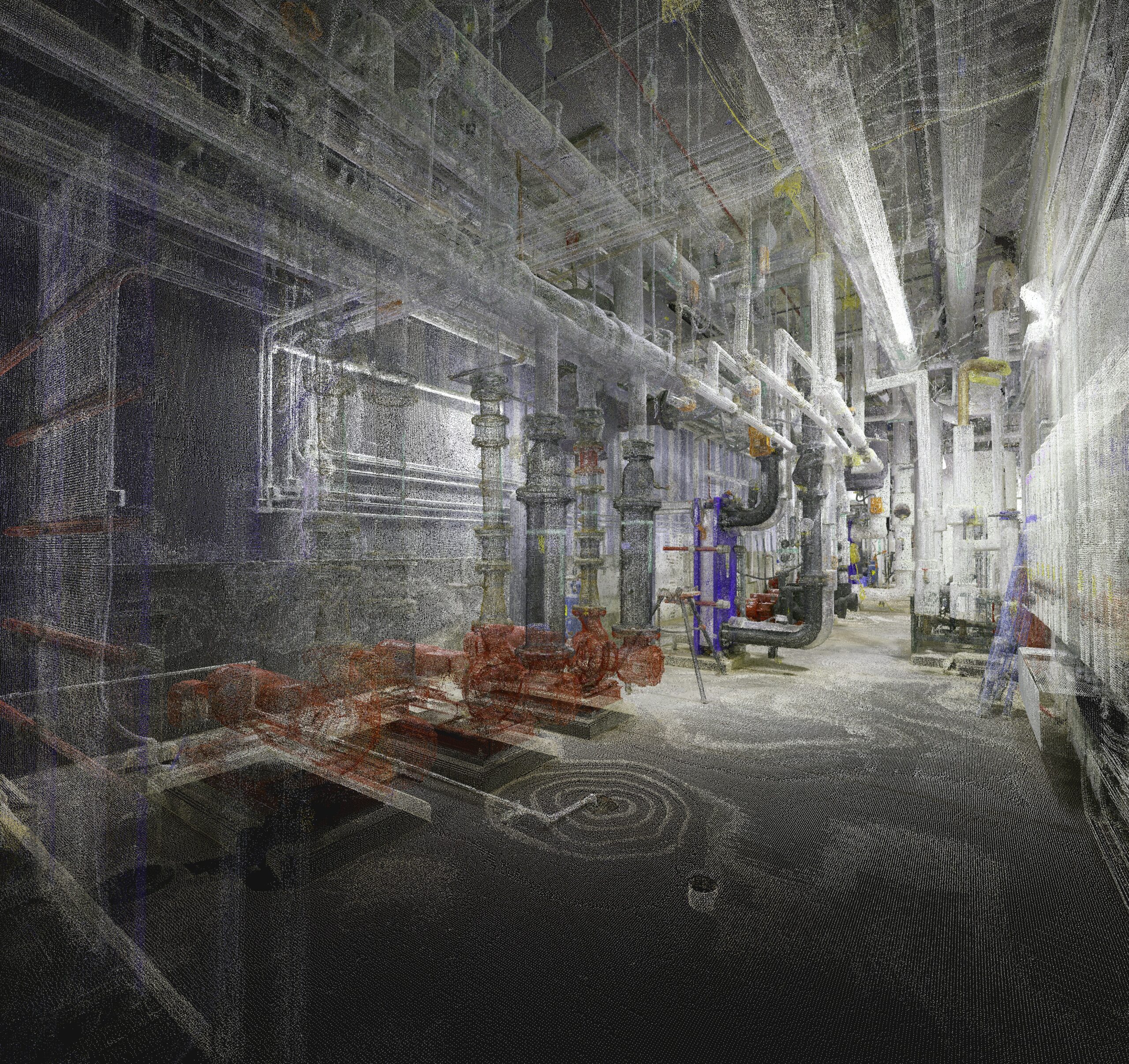
The outcome in Florida reflects the benefits the company has seen by applying laser scanning to projects across its portfolio. “For a data center project in Des Moines, our electrical team is working towards using scans from a similar finished facility to use as a template on the new center,” Marriott says. “The level of accuracy means we can move forward with component prefabrication on the new facility much sooner and with confidence.”
The ability to work concurrently on MEP and façade fabrication versus a traditional, slower workflow is a big factor in project estimates. “It’s an advantage,” Marriott states. “Knowing we can track and hold tolerances with precision means we can shave months off a delivery schedule.”
Processing Speed Maximizes Efficiency
Marriott believes Weitz holds another advantage that’s allowed them to leverage technology better: the laser scanning hardware and software they rely on. “We performed a full evaluation on a lot of different systems. In my view, it comes down to how much time you spend processing data. For every hour you scan, you can spend 10 hours processing the data. That’s expensive.
“With Leica, we cut that number by at least half. Plus, we extract more quality data. We can even send an estimator with no previous scanning experience out to a site to scan. These tools can be applied to so many different situations. The ease and versatility continue to open eyes here.”
To learn more, connect with a Leica Geosystems reality capture specialist.