As overall construction spending continues to expand, general contractors increasingly face the challenge of meeting tight project deadlines while reducing rework and staying on budget. To achieve these goals, GCs are investing in reality capture technology and visualization tools to provide accurate, measurable data for in-field verification and quality control.
The Weitz Co., which specializes in delivering large-scale projects under fast-track design-build delivery methods, is taking reality capture a step further.
Weitz provided BIM coordination and virtual design and construction (VDC) services for a new undergraduate residential complex in Florida. By applying the latest innovations in VDC capabilities and laser scanning technology, the company kept pace with a pressing timeline, achieving a BIM level of development (LOD) 500 model while ensuring that subcontractor work met quality control as the buildings were constructed. In demonstrating the ability to provide near-real-time access to accurate, measurable as-built data, the project sets a new standard for best practices in VDC and BIM.
On-Demand Scanning Provides Crucial Insights
The undergraduate residential complex involves the construction of four buildings, including an honors college and undergraduate housing.
Initially, project leadership for the university wanted a LOD 500 model compiled from post-installation subcontractor models. Weitz suggested a more collaborative approach: Assigning a dedicated VDC specialist to the project who would capture as-builts with laser scanning as the elements were installed. The 3D point cloud generated from the scans would then be compared to the designs as construction progressed to identify any issues that could cause delays or cost overruns.
Jonathan Jailal, VDC engineer II at Weitz, says, “This was a time and money saving proposition to give them the best deliverable possible for the lowest cost.”
Above: 1) Logan McGuinness, VDC Manager for Weitz, uses the Leica RTC360 laser scanner to capture a 3D color point cloud of an area in under two minutes at the touch of a button with in-field preregistration of the data. 2) Jonathan Jailal, VDC engineer II at Weitz, uses the Leica BLK2GO handheld imaging laser scanner to capture complete scan data on an entire slab in minutes for an efficient as-built data capture workflow. 3) A point cloud as-built of a pre-pour slab captured with the BLK2GO.
Weitz chose to use the Leica BLK2GO and RTC360 due to the scanners’ combination of speed and quality of measurement, along with the technology manufacturer’s reputation for reliability, service, and support. The handheld BLK2GO imaging laser scanner captures the 3D environment as the operator walks through a space. The tripod-mounted RTC360 can create a 3D color point cloud of an area in under two minutes at the touch of a button with in-field preregistration of the data. Used together, the instruments provide significant flexibility to capture and communicate as-built information on-demand.
In addition to laser scanning, Weitz also provided 360-degree photo documentation and aerial progress photos.
Slab Scanning Done Fast
At the project’s outset, Jailal scanned slabs before concrete was poured to capture the locations of rebar, conduits, sleeves, penetrations, and blockouts. These scans, along with all of those taken through the project, were uploaded into a central repository in Procore software where they could be accessed by stakeholders throughout the entire construction process.
The point cloud showed the as-built data down to millimeter precision, and the scans were survey controlled to align with the initial BIM model, helping to ensure that the as-built matched the design.
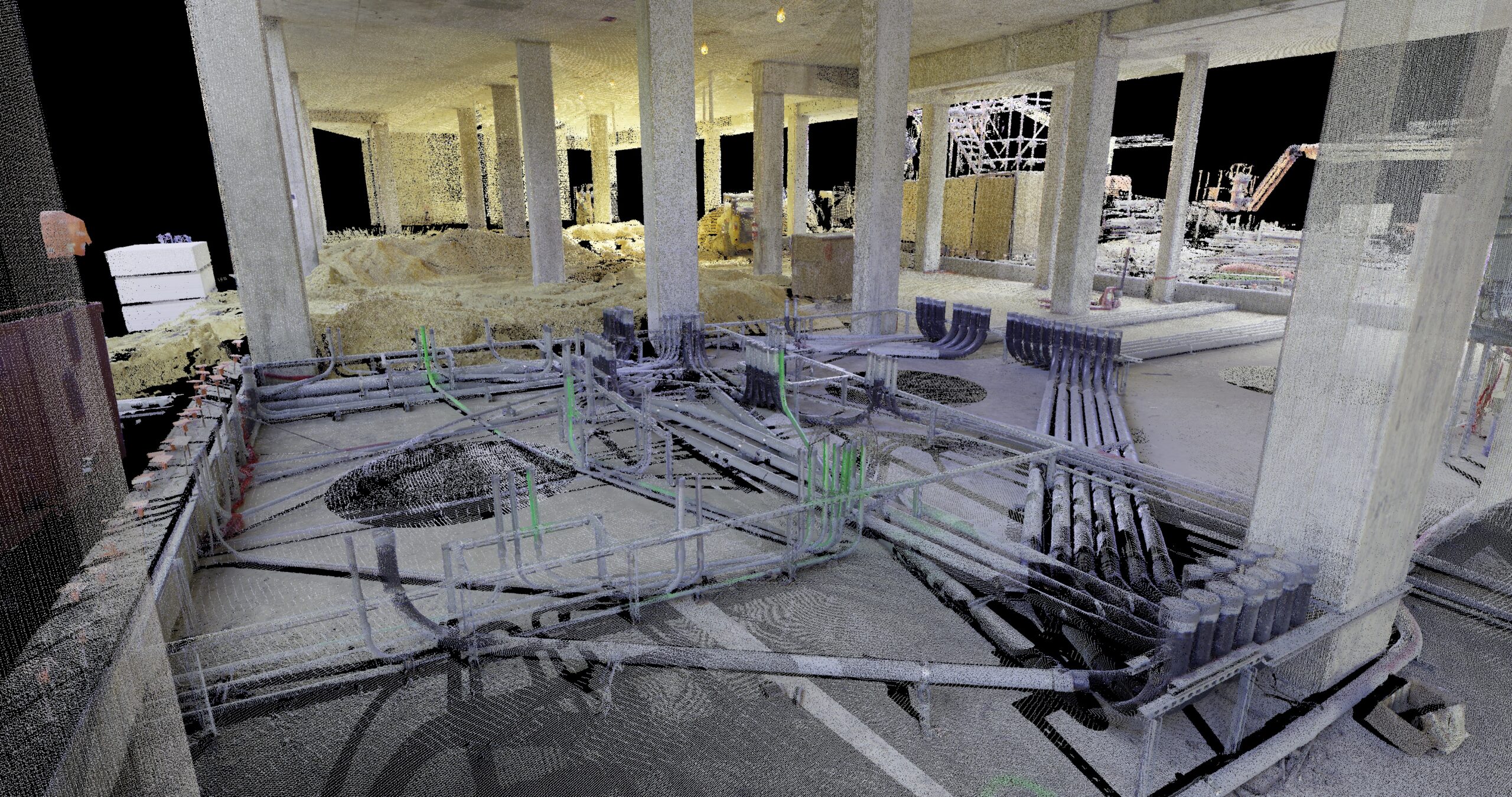
As important as the scan data was to the project, however, the timing was crucial.
The project had such a tight schedule that “there were days when we had less than a few hours between formwork and concrete pours, or between the electrical getting finished on the deck and concrete getting poured,” says Logan McGuinness, VDC Manager at Weitz.
The weather also created challenges. “During summertime, the area had a lot of rain and lightning storms,” says Jailal. “If lighting was within 10 miles, we shut down all exterior work. So there were instances where I only had about 10 minutes to scan what I needed.”
Using the BLK2GO handheld laser scanner enabled Jailal to capture complete scan data on an entire slab in minutes for an efficient as-built data capture workflow.
Scanning for Quality Control
In addition to the slab scanning, Weitz captured scans throughout the project to ensure that the as-built continually matched the BIM design.
Jailal scanned underground plumbing to ensure that it conformed to the design work and to coordinate pipe placements between subcontractors. He also captured in-wall elements such as electric conduits, studs, and blocking before drywall installation, as well as overhead installations for the placement of mechanical pipe, ductwork, fire protection, plumbing, and electrical conduit and cable trays.
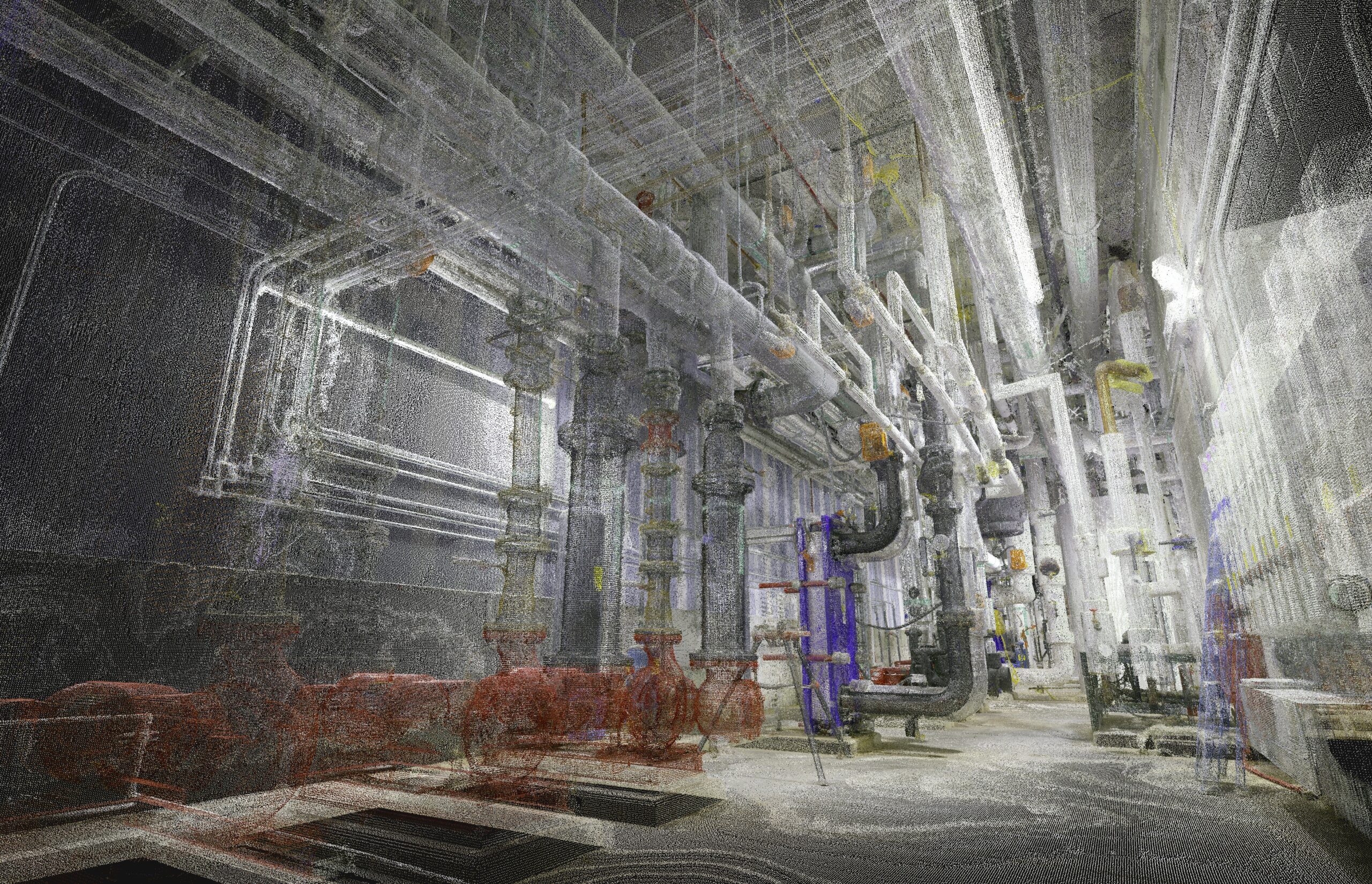
Jailal scanned the building interior weekly with the BLK2GO. He used the RTC360 to fill in the dataset with higher density as well as to complete longer-range scans such as corridors and exterior scans.
In contrast to traditional 2D as-built drawings, the laser scans provided a measurable, navigable 3D view of the entire building. Jailal easily overlaid the data into the model to ensure that the as-built work matched the design and detect potential conflicts with future installations.
Slicing Down Rework
By regularly scanning the as-built structure while subcontractors completed work, Jailal provided the team with almost instant insight into any deviations from the design and whether they would impact future work.
In one case, a cooling tower needed to be placed within a few days after the reinforced concrete pedestal was poured.
“I scanned the rebar before the formwork and brought it into the model,” he says. “It was a foot and a half lower than it should have been. I was able to get that information to the project team within the same day, and the next day the subcontractor corrected it. The concrete was able to be poured the same day as planned.”
Without that scan and quick transfer of information, the mistake likely would not have been caught until the concrete was poured and the cooling tower was placed on the pedestal.
“And once the cooling tower is on site, where are you going to put it to redo the work?” he asks.
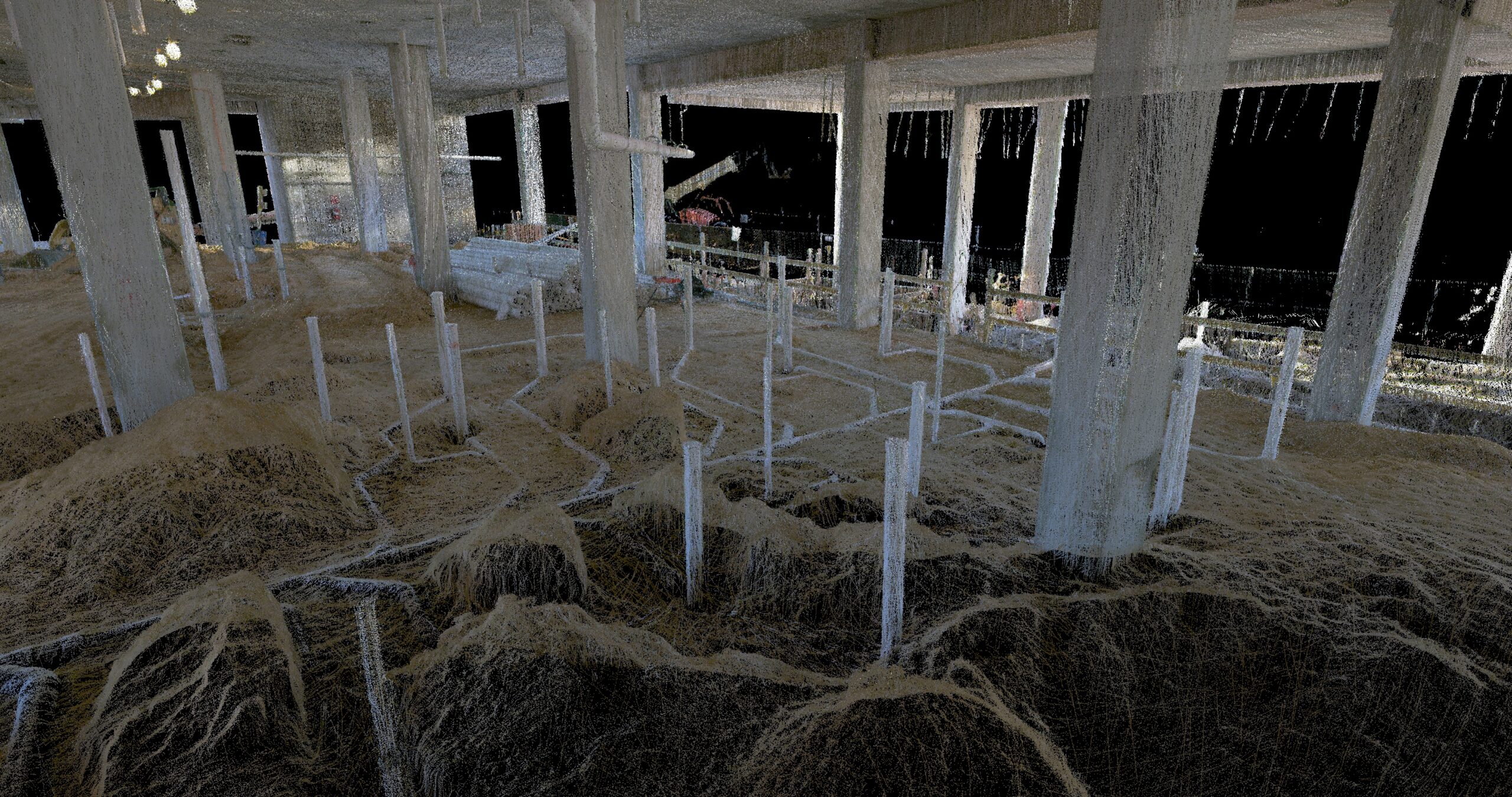
In another instance, a curtain wall was designed to fit under a cantilevered slab, but an exterior framing contractor noticed that the concrete deviated from one end to the other, which could interfere with the installation of exterior panels. Scanning helped verify that the curtain wall would fit, and the design team discussed whether the exterior plans needed to be adjusted. Having the visualization of the point cloud simplified collaborative problem-solving.
Jailal notes how this aspect of laser scanning also provides value for resolving disputes between subcontractors. Instead of getting bogged down with arguments and finger-pointing when work is out of tolerance, the scan can provide an accurate frame of reference.
“Once the laser scan data is presented, nobody questions it, and they move forward to fix any issues,” he says.
Next Stop: A VDC Specialist for Every Project
By assigning a dedicated VDC engineer to the project and scanning on-demand with the BLK2GO and RTC360 laser scanners, The Weitz Co. kept pace with a pressing timeline and captured the as-built data of the housing project while providing in-field verification and quality control. This approach maintained quality control throughout the process and allowed Weitz to create a robust point cloud of the as-builts that the university will be able to use for years to come for repairs and renovations.
Although the project did encounter some construction delays due to weather and supply chain disruptions, two of the four buildings were completed on time in summer 2023. Notably, the project was able to stay within the original cost estimate of $187 million.
As building construction increasingly shifts from traditional methods into digital construction, VDC approaches must also evolve. The ability to gain new efficiencies and insights with near-real-time access to accurate, measurable as-built data brings the next level of fast-track project delivery within reach.
To explore laser scanning solutions and discuss your needs with a building construction specialist, contact us.
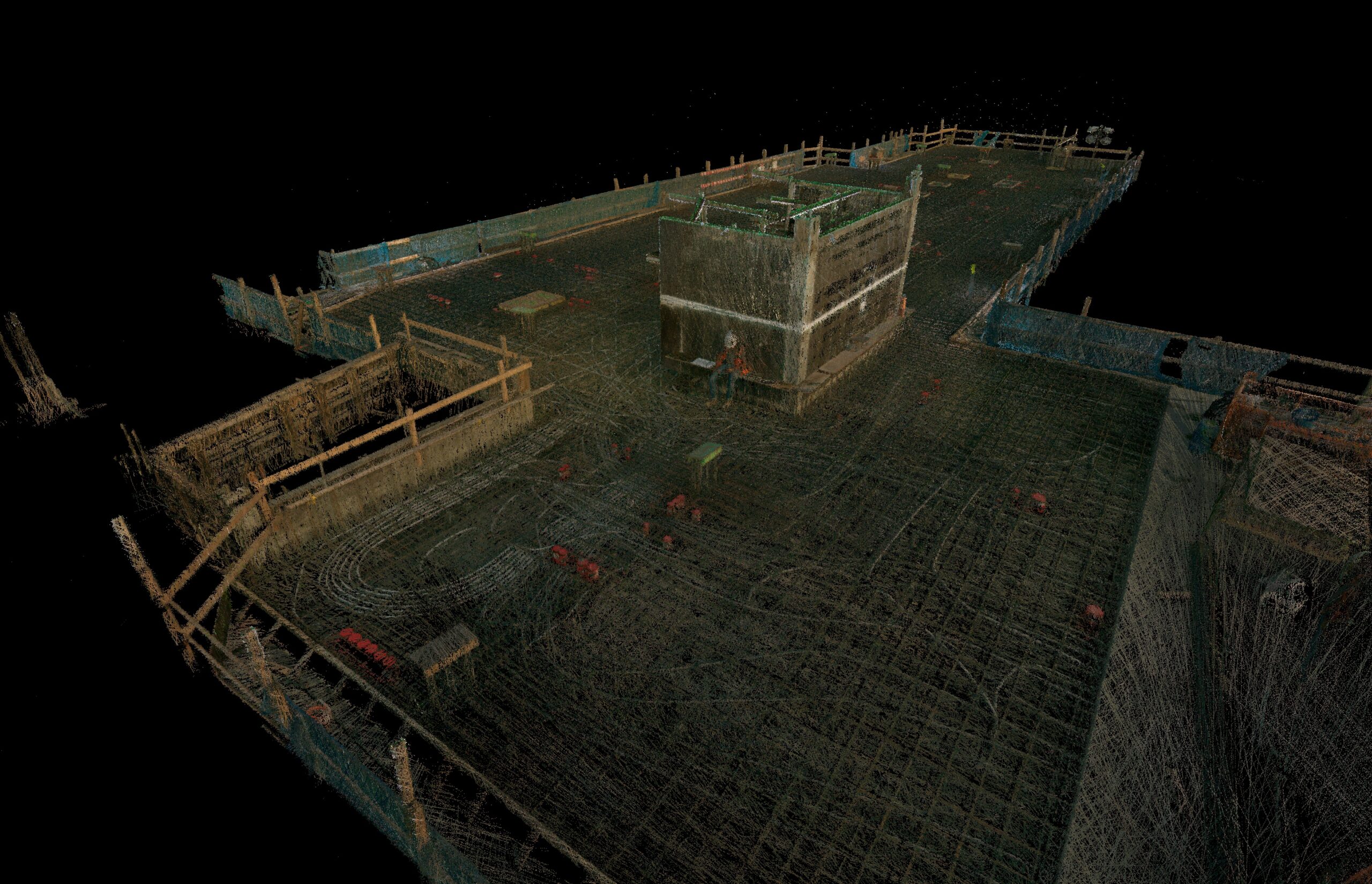