Inspecting the curtain wall on a multistory building is not a job for the faint of heart. Workers spend hours in lifts or on high-rise swing stages, taking photos and measurements to document potential problems. The work is expensive, time consuming and dangerous. The progressive leaders of Brasfield & Gorrie, one of the largest privately held construction firms in the U.S., were determined to find a better way.
In 2013, the firm was tasked with completing the 12-story Grandview Medical Center in Birmingham, Ala., after new owners resumed work on the construction project following a decade-long hiatus. Before construction work could begin, thorough inspections were needed to document existing conditions of the building’s interior and exterior, including the convex-shaped curtain wall. Although the team still had to rely on traditional manual curtain wall inspection methods for this project, they also wanted to explore a new possibility to find out whether it would be a viable alternative in the future.
“We were trying to come up with a way that would be safer and more cost effective, and so we had the idea of using a drone,” said Susan Stabler, Brasfield & Gorrie senior project manager. “Since we knew that wasn’t industry standard yet, we thought of the School of Building Science at Auburn University.”
Fast, Accurate Photogrammetry
Auburn University researchers had already been studying applications for unmanned aircraft systems (UAS) in building construction applications. Also called unmanned aerial vehicles, or UAVs, the small, unpiloted aircraft can capture high-resolution imagery for surveying and mapping. Rotary systems like the Aibot X6 hexacopter from Leica Geosystems are easy to maneuver and can hover in place, allowing them to be used for complex inspection tasks that require high-accuracy documentation.
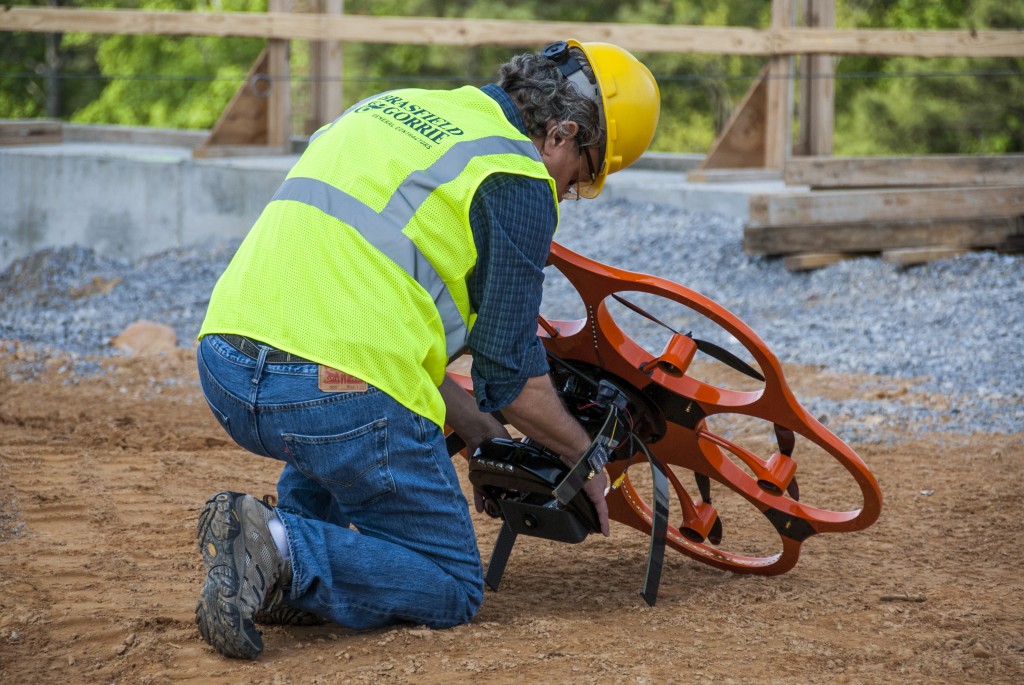
The team agreed that the Grandview Medical Center would be a good pilot project to test the capabilities of the technology. Working closely with Brasfield & Gorrie as well as consulting firm CCLD Technologies Inc., the Auburn University team first used a Leica ScanStation C10 ground-based laser scanner to quickly capture several million highly accurate measurements of the curtain wall and part of the interior of the building in the form of a point cloud. This information was used to develop a baseline for a 4,000 square foot section of the existing curtain wall.
CCLD then flew an Aibot X6 equipped with a digital camera along the same section of curtain wall as well as the parking garage in a predefined grid to capture georeferenced high-resolution images and videos. The documentation process took a fraction of the time that would have been required for manual inspection. The resulting high-definition photos and videos were linked to the building information model (BIM) produced by Brasfield & Gorrie’s Virtual Design and Construction (VDC) group to provide a record of the current conditions. By selecting a link, inspectors and waterproofing consultants would be able to view an image of that particular section of the curtain wall and thus could get close-up views of every inch of the exterior skin of the building in the test area. This would make it much easier for them to evaluate problems and formulate corrective action plans.
The UAS-captured photos were then transformed into point clouds and models using photogrammetric software. These were compared to the point clouds generated by the terrestrial laser scanner to assess the accuracy of the UAS-captured images. The LIDAR-generated point cloud for the test area was assigned a reference plane, and the photogrammetric generated point cloud was overlaid and matched to this plane. A single band of curtain wall was then isolated, and a plane section was selected to compare the profiles of the two point clouds.
Although the LIDAR-generated point cloud was more accurate, the planar dimensional error for the photogrammetry-generated point cloud was only plus or minus 9/16th of an inch (1.5 cm), which falls well within the tolerance specified for most projects.
Safe, Complete Inspections
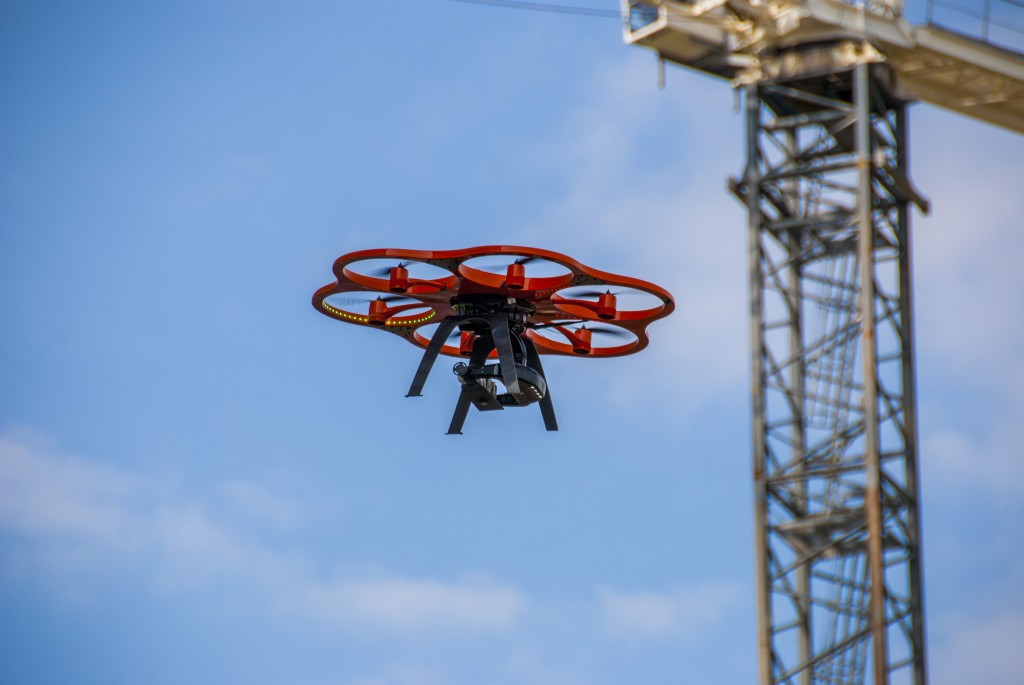
Although the test was only conducted on small sample area of the building due to regulations limiting the commercial use of UAS, this pilot project demonstrated how construction firms could avoid sending workers up on scaffolding by using an accurate, professional-grade UAS to capture high resolution images of the curtain wall. The aerial images were successfully integrated into existing BIM models, allowing stakeholders to conduct detailed inspections at close range. And with photogrammetric software, the UAS-generated data was converted to precise point clouds and 3D models. On an actual project, this information would be a valuable addition to existing building documentation.
“Inspecting the exterior skin of buildings using swing stages, lifts and cranes is filled with safety issues and is extremely time consuming, with no obvious way to capture, document and organize the physical building for approval,” said Russell Gibbs, regional director of VDC for Brasfield & Gorrie. “This pilot project with the Aibot X6 showed how we could capture an image directly tied to a location on our model to substantially improve the process. This new technology opens many new, innovative opportunities in construction.”